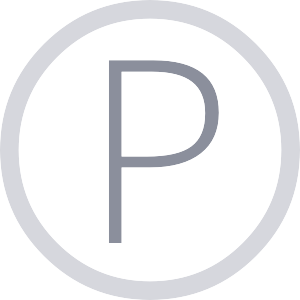
Who do you trust?
The independent technology service assisting industry to improve process, chemistry, productivity, sustainability. For Chemicals, Mining, Paper, Metals, Alumina, Food, Utilities, Retail and other Industries.
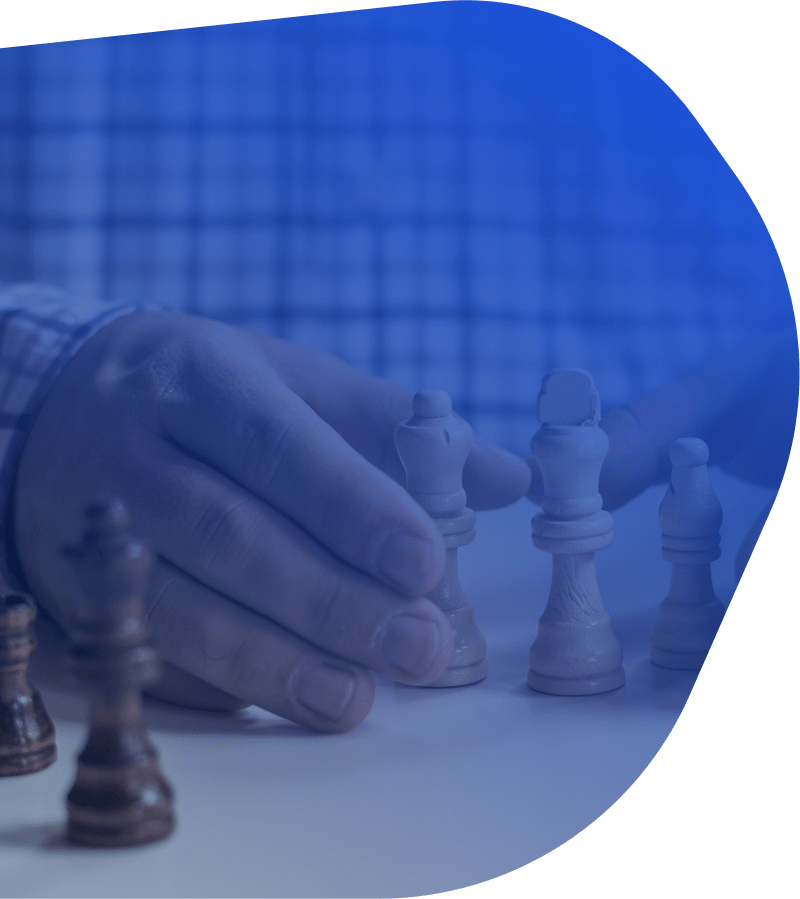
Process Variance
Process variance is a result of the interaction of multiple factors or variables. If allowed to drift over time or, suddenly change adversely, it can result in significant losses to the industrial site. Process Chemistry Analytics (PCA) focuses on the industrial process and chemistry, whilst also considering the effect of other production factors. Our independent “statistical thinking” – the deciphering of patterns in data using proven, peer-reviewed computer algorithms – can be applied to many different industrial processes.
Some important factors are changes in chemical treatment, personnel or supplier. Changes in multiple operational factors are considered, including plant, raw materials, water quality, equipment, control strategies, chemical addition points, dilution, hydrodynamics, etc.
Whether it is a mine site, a paper mill, metals, alumina, a food or beverage plant or, other industrial site, this service assists in separating out the effects of your process and chemistry from the many other production and mechanical factors.
In order to make decisions with confidence, management of industrial sites need independent “statistical thinking” to balance and augment expert intuition. PCA is independent of suppliers and provides an impartial assessment. PCA applies industry process and chemistry knowledge, advanced data management, statistical and graphical techniques to verify and benchmark your process and chemistry. This independent “statistical thinking” is then summarised in a PCA report.
All PCA reports are based on the site’s own production data, whether from online process control sensors or manually collected data sets. High security cryptography is used to prove a PCA report originated from PCA and has not been altered by a third party (digitally signed SHA-256 checksum, as designed by the United States National Security Agency – the same technique that software distributors use to verify the integrity of file downloads).
Therefore, the client can have confidence it is the original report from PCA, based on the industrial site’s own data.
Ongoing Reports for Industrial Sites and Suppliers
Enhanced reports on your chemical, equipment and control strategies. These can be on a monthly, bimonthly or less frequent basis. For example, for regular process and production review and, meetings with suppliers. Industrial sites can benefit. Suppliers can benefit from this independent service from PCA to demonstrate to industrial sites that they have confidence in their technology.
Reports on Plant Trials of New Chemicals, Equipment and Control Strategies
These can be prepared for the supplier or the industrial site or both. Typically they involve comparing production performance before, during and after the trial. They enable you to reliably quantify the effects of new technologies.
Benchmarking Reports
These can be prepared for the supplier or the industrial site or both. For example, to compare performance of one industrial process at different times. Or, with permission, to compare performance of a specific technology at two or more similar industrial sites. What is the industry average performance for a specific technology? What is the variance in performance?
Troubleshooting Reports
For those times when the site is unhappy with current performance and needs to diagnose process chemistry issues.
Reports on new AI (black box) control systems
Some chemical and equipment suppliers are now offering proprietary AI based control systems, but only if you purchase their chemicals or equipment. PCA can evaluate these systems and mitigate the risk of being tied to a particular supplier.
Neural network and hybrid predictive modelling and control
Longer-term projects are available in conjunction with leading universities. These and various multivariate and non-parametric statistical techniques are the basis of so-called AI based control systems. Industrial sites can develop their own systems without being tied to a supplier.
Get Started Today
There is a need in the industrial marketplace for a trusted, independent, data-based service to assist suppliers and industrial sites to improve process and chemistry performance. PCA’s mission is to provide your business with that service.